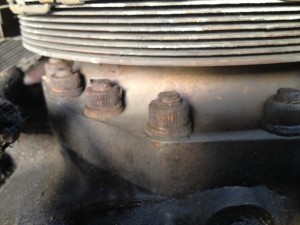
The first problem to over come to remove cylinder, is the 40 point spline nuts used by Bristol to secure the cylinder, we tried for many hours to track down a base nut spanners , so in the end we decided to make one.
First remove one of the nuts using vice grips , then measure the size of the spline and drill some plate to suit, heat up to red hot
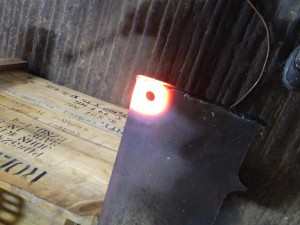
Then use the nut as a broach and press into the plate,
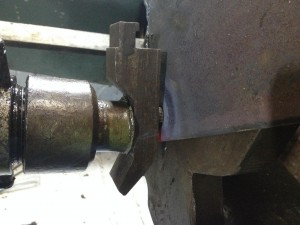
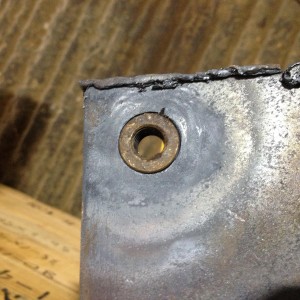
Cut out and weld to an old 3/8″ extension
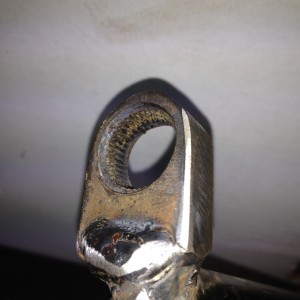
Next heat up to cherry red and submerge into carbon , in our case some crushed up BBQ bricks! and allow to cool to case harden.
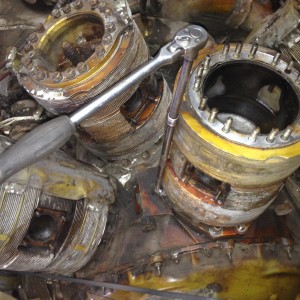
Job done works a treat.
Next job was to make a puller plate to attach to the cylinder and a plate that fits down the bore so we can push on the piston evenly.
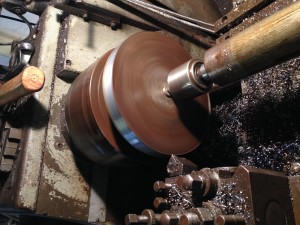
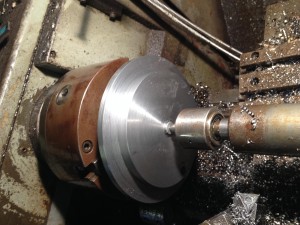
A bit more milling work for Pete!
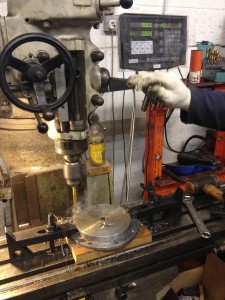
First we tried 15 tonnes to remove the cylinder.
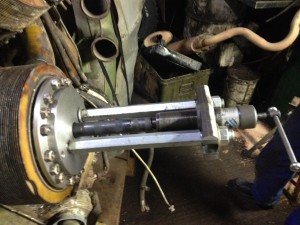
No movement, so we stepped up to 30 tonnes!
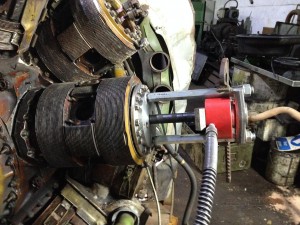
That did the trick, as soon as it started to move we could use threaded rod and a windy gun to pull off the cylinder.
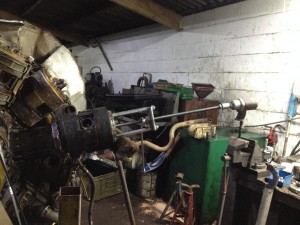
That’s one down , thirteen to go!